Is Batch Mixing The Solution For You?
By Isaac Fletcher, contributing writer, Food Online
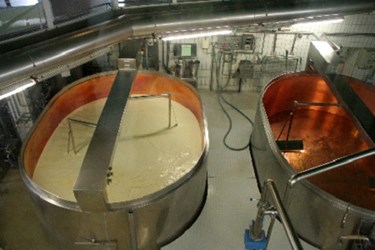
To get the most out of your operation, it is essential to make careful considerations when choosing production equipment. Although mixing may seem relatively straightforward, making the choice between batch and continuous mixing can have a significant impact on productivity and efficiency
When it comes to picking an industrial mixer for your processing operation, there are some important factors to consider. Mixers come in a range of shapes, sizes, arrangements, and modes of operation, but will generally fit into one of two categories: batch or continuous. Batch mixing is performed by loading all materials into the mixer together or in a predetermined sequence. The inputs are then mixed until a homogenous material is created and removed from the mixer as a single batch.
On the other hand, continuous mixing is typically dedicated to a single, high-volume product. With this method, ingredients are continuously fed into the mixer, mixed together, and moved from the charging port to the discharge nozzle where the mixed material is continuously discharged. While the output of a batch mixer is measured by its weight per batch, continuous mixers’ output is measured by its weight per hour.
When determining which type of mixer would best fit your operational needs, you should consider factors such as:
- The quantity of material to be mixed
- How much homogeneity is required throughout the product mix
- Pre-mixing operations and material-handling equipment
- Post-mixing operations
- Whether or not there are any multiple product formulation requirements
While some kinds of mixers can be adapted for use in both continuous and batch mixing, others are only suitable for one. For example, plow mixers and ribbon blenders can be applied to operations for both batch and continuous mixing, but tumble blenders are suited only for batch mixing operations.
Batch Mixing
As noted previously, batch mixing is generally made up of three sequential steps: weighing and loading ingredients, mixing, and discharging the mixed material. Mixing cycle times can range from just a few seconds with high-intensity units, to many hours when additional processing elements are required. Once mixed to the necessary level of homogeneity, the material is discharged from the vessel. To avoid operational bottlenecks, it’s important to discharge finished materials quickly and make sure mixers are not being used for storage purposes.
The total batch time is contingent upon the time required to load the material into the mixer, the mixing cycle, and the discharge time. Additionally, in applications where product contamination between batches can occur, there will be further time requirements for cleaning and sanitizing.
Types of Batch Mixers
There is a variety of batch mixers to choose from to meet your specific operational needs:
- Tumbler Blenders
Octagonal Blender, Double Cone Blender, V-Blender
- Fluidization Mixers
Plow Mixer, Double-Shaft Paddle Mixer
- Convective Mixers
Ribbon Blender, Vertical Screw Blender, Sigma Mixer, Paddle Blender, Planetary Mixer
Batch Mixing Applications
Batch mixing is the method of choice for manufacturers that produce in small to medium capacities. Factors influencing which mixer to be implemented include mixing duration, size and shape of the mixer, and operating conditions. Some of the preferred applications include operations where:
- Many formulations are produced on the same line
- The properties of ingredients change over time
- There is a low amounts of production quantity
- Strict control of mixed material composition is necessary
Batch Mixing Advantages
Some advantages of batch mixing include:
- Stringent control of material quality
- Ability to trace products on a batch-by-batch basis
- Reduced operating costs when used in small to medium capacities
- Production and mixing time flexibility
Batch Mixing Limitations
The disadvantages of batch mixers include:
- Poor economic efficiency when large quantities need to be mixed
- Requirement for higher amounts of labor compared to continuous mixing